Georgia CNC Machine Shop
Georgia CNC Multi-Axis Milling
Our milling centers are all high speed and have 4 or 5-axis capability. This enables us to complete parts in two fully automated operations where other machine shops may have to use as many as six, potentially inaccurate, manually placed operations.
We can easily mill features at any combination of compound angle relative to any face on a part using 3+2 axis milling. Our CAD/CAM applications and milling centers are also capable of full motion 5-axis milling to achieve any surface contouring requirement.


CNC Multi-Axis Milling / Turning
What Our Clients Say:
"In partnering with Cornertech over the years I have always found them easy to work with, quick to turn quotes and very proactive with innovative techniques & tooling designed to turn large volume quickly needed orders with a high degree of precision."
Mike Gallagher
Procurement Manager
-
Jormac Aerospace
In the manufacturing landscape, CNC machine shops have emerged as front-runners in the realm of precision, efficiency, and innovation. But what exactly constitutes these highly specialized workshops, and how has digitalization revamped the conventional processes? Let’s embark on a deep dive.
The Anatomy of a Georgia CNC Machine Shop
At the heart of every Georgia CNC machine shop is a fundamental goal: the precise subtraction of materials from a raw form to produce meticulously crafted parts. Achieving this involves a plethora of tools and equipment:
- Milling Machines: These tools employ rotary cutters to remove material and can be operated manually or via CNC.
- Machining Centers: Highly automated machines capable of performing multiple machining operations.
- Lathes: Spinning machines designed for detailed shaping of raw materials.
- Grinding Machines: Precision tools for creating smooth finishes or close tolerances on metal parts.
- Bandsaws and Drill Presses: Essential for cutting and drilling operations.
- EDM Equipment: Implements electrical discharges to mold hard metals and intricate shapes.
- Surface Finishing Tools: Tools that enhance a component’s finish post-machining.
- Coordinate Measuring Machines (CMMs): Precision devices for measuring the physical geometrical characteristics of an object.
Equally vital to a CNC machine shop’s arsenal is the computational power, typically equipped with CAD software, to turn intricate designs into real-world components.
The Digital Transformation of CNC Machining
Digitalization has ushered in a new era for CNC machine shops. Where once the emphasis was on the hands-on expertise of operators, today, the reliance has shifted to CNC’s pinpoint accuracy guided by complex computer algorithms. This paradigm shift can be attributed to several breakthroughs:
- Transition to G-Code: The seamless transformation of 3D designs into G-Code allows machines to understand and replicate detailed designs with unmatched precision.
- 5-Axis CNC Mills: By introducing machines that can operate on five different axes simultaneously, intricate tasks that once took hours can now be completed in minutes.
- Balancing Act between Manual and CNC Machining: Contrary to popular belief, the digital age hasn’t rendered manual machining obsolete. While CNC offers unmatched precision and repeatability, manual machining retains its place for simpler, less intricate projects.
Safety Protocols in a Georgia CNC Machine Shop
A well-run CNC machine shop prioritizes safety above all. This includes:
- Appropriate Attire: Ensuring protective gear such as safety glasses, gloves, and closed-toed shoes are worn at all times.
- Focused Operation: A zero-distraction policy when handling machines.
- Constant Supervision: Machines should never be left running unsupervised.
- Handling of Flammable Materials: Implementing rigorous protocols for the storage and use of combustibles.
- Emergency Preparedness: Ensuring clear pathways to emergency exits and regular safety drills.
Choosing the Right CNC Machine Shop for Outsourcing
Outsourcing to a CNC machine shop is a significant decision and demands due diligence. Key criteria include:
- Reliability: Can they deliver on promises consistently?
- Industry Experience: How well do they understand the nuances of your domain?
- Value Proposition: Their pricing should reflect the quality of their services.
- Confidentiality Measures: The use of Non-Disclosure Agreements (NDAs) to ensure your designs and data remain secure.
- State-of-the-Art Equipment: Their machinery should reflect current industry standards.
To wrap up, Georgia CNC machine shops today are more than just a cluster of machinery. They represent the zenith of precision engineering, enhanced by digital innovation, and are pivotal in driving the manufacturing sector forward.
Georgia CNC MANUFACTURING Production
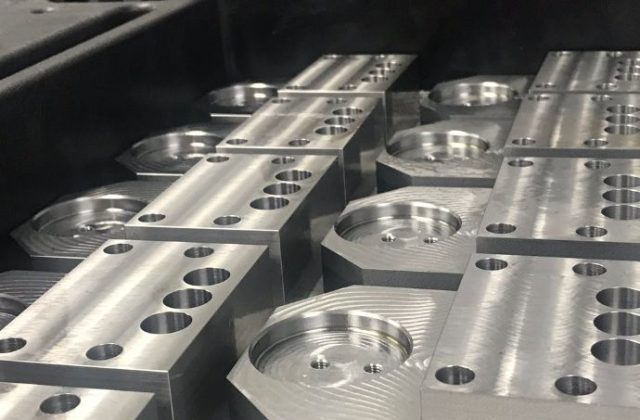
At Cornertech, we consider all production volumes first understanding the needs and goals of our clients then developing solutions that will optimize production; keeping cost down and making sure we hit delivery dates.

For larger production runs, we manufacture our own fixtures to hold multiple parts during production in order to optimize efficiency and keep the cost down for our clients.